A tantalum ingot is a solid, rectangular block of tantalum metal produced through various metallurgical processes. Tantalum, a rare and valuable transition metal, is known for its exceptional properties, including high melting point, excellent corrosion resistance, and good ductility. These ingots serve as the primary form for storing and transporting tantalum, which is later processed into various products for use in diverse industries. The unique characteristics of tantalum make it an essential material in modern technology and manufacturing.
How is a tantalum ingot produced?
The production of tantalum ingots involves a complex series of steps, starting from raw ore extraction to the final melting and casting process. The primary source of tantalum is the mineral columbite-tantalite, also known as coltan. The production process typically includes the following stages:
- Ore extraction and processing: Tantalum-bearing ores are mined from the earth and then undergo initial processing to concentrate the tantalum content. This often involves crushing, grinding, and various separation techniques such as gravity concentration or flotation.
- Chemical processing: The concentrated ore is then subjected to chemical treatments to further purify and extract tantalum. This may involve acid leaching, solvent extraction, or other chemical processes to separate tantalum from other elements present in the ore.
- Reduction to metal: The purified tantalum compound is then reduced to metallic form. This is often done through processes such as electrolysis or chemical reduction using agents like sodium or hydrogen.
- Powder consolidation: The resulting tantalum metal powder is compressed and sintered to form a solid mass. This step helps to increase the density and structural integrity of the material.
- Electron beam melting: The consolidated tantalum is then melted using an electron beam furnace. This high-temperature, vacuum-based process helps to further purify the metal and remove any remaining impurities.
- Casting and solidification: The molten tantalum is cast into molds to form ingots of desired shapes and sizes. The metal is allowed to cool and solidify under controlled conditions to ensure uniform structure and properties.
- Quality control and finishing: The solidified ingots undergo various quality control checks, including chemical analysis, physical property tests, and visual inspections. They may also be subjected to additional processing such as surface cleaning or machining to meet specific customer requirements.
The production of high-purity tantalum ingots requires advanced technology and strict quality control measures. The process is energy-intensive and requires significant expertise to ensure the final product meets the stringent standards required for various applications. The resulting ingots serve as the starting material for further processing into various tantalum products used across industries.
What are the main applications of tantalum ingots in electronics?
Tantalum ingots play a crucial role in the electronics industry, serving as the raw material for various components and applications. The unique properties of tantalum, such as its high capacitance, excellent conductivity, and stability, make it an invaluable material in modern electronic devices. Some of the main applications of tantalum ingots in electronics include:
- Capacitors: One of the most significant uses of tantalum in electronics is in the production of capacitors. Tantalum capacitors are known for their high capacitance in a small volume, stability over a wide temperature range, and long-term reliability. These characteristics make them ideal for use in portable electronic devices, automotive electronics, and aerospace applications. Tantalum ingots are processed into thin foils or powders, which form the basis of these high-performance capacitors.
- Sputtering targets: Tantalum ingots are used to create sputtering targets, which are essential in the production of thin films for various electronic components. In the semiconductor industry, tantalum thin films are used as diffusion barriers and gate electrodes in integrated circuits. The sputtering process involves bombarding the tantalum target with high-energy particles to deposit a thin layer of tantalum onto a substrate.
- Heat sinks: Due to its excellent thermal conductivity and high melting point, tantalum is used in the production of heat sinks for high-power electronic components. These heat sinks help dissipate heat efficiently, ensuring the proper functioning and longevity of electronic devices.
- Electrical contacts: Tantalum's resistance to corrosion and good electrical conductivity make it suitable for use in electrical contacts in various electronic devices. These contacts are crucial for maintaining reliable electrical connections in circuits and components.
- Radio frequency (RF) shielding: Tantalum's ability to absorb certain electromagnetic frequencies makes it useful in RF shielding applications. This property is particularly valuable in sensitive electronic equipment and communications devices.
- Vacuum tubes: Although less common in modern electronics, tantalum is still used in specialized vacuum tubes for high-power applications, such as radio transmitters and scientific instruments.
- Semiconductor manufacturing: Tantalum plays a role in the production of various semiconductor materials and devices. It is used in chemical vapor deposition (CVD) processes and as a component in certain alloys used in semiconductor manufacturing equipment.
The versatility of tantalum in electronics stems from its unique combination of properties, including high melting point, excellent corrosion resistance, and good ductility. These characteristics allow tantalum-based components to withstand harsh operating conditions and maintain their performance over extended periods. As the electronics industry continues to evolve, with a focus on miniaturization, increased efficiency, and improved reliability, the demand for tantalum and its applications in this sector is likely to grow.
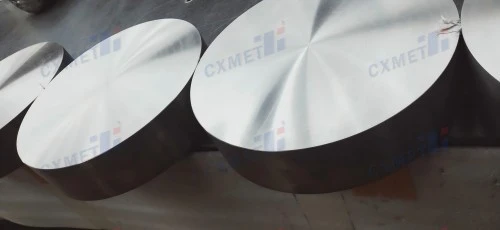
How does the aerospace industry utilize tantalum ingots?
The aerospace industry is another significant consumer of tantalum ingots, leveraging the metal's exceptional properties to enhance the performance and reliability of various aircraft and spacecraft components. Tantalum's high melting point, excellent corrosion resistance, and good strength-to-weight ratio make it an ideal material for numerous aerospace applications. Here's a detailed look at how the aerospace industry utilizes tantalum ingots:
- Jet engine components: Tantalum is used in the production of various parts in jet engines, particularly in areas exposed to high temperatures and corrosive environments. Tantalum alloys are used to create turbine blades, nozzles, and other critical components that must withstand extreme conditions. The metal's high melting point (3,017°C or 5,463°F) allows these parts to maintain their structural integrity under the intense heat generated by jet engines.
- Rocket nozzles: In spacecraft and missiles, tantalum is used to manufacture rocket nozzles. The metal's resistance to erosion and ability to withstand high temperatures make it ideal for this application, where the nozzle must endure the extreme heat and pressure of rocket exhaust gases.
- Heat shields: Tantalum's excellent heat resistance properties make it valuable in the production of heat shields for spacecraft. These shields protect the vehicle and its occupants from the intense heat generated during atmospheric re-entry.
- Structural components: Tantalum alloys are used in various structural components of aircraft and spacecraft where high strength-to-weight ratio and corrosion resistance are crucial. This includes parts of the fuselage, wing structures, and landing gear components.
- Fasteners and fittings: Specialized fasteners and fittings made from tantalum or its alloys are used in areas of aircraft and spacecraft that require high strength and corrosion resistance. These components ensure the structural integrity of the vehicle under various operating conditions.
- Hydraulic systems: Tantalum's corrosion resistance makes it suitable for use in certain components of hydraulic systems in aircraft. This is particularly important in systems that use corrosive hydraulic fluids or operate in harsh environments.
- Electrical and electronic components: As in other electronics applications, tantalum is used in aerospace-grade capacitors, resistors, and other electronic components. These components must meet stringent reliability and performance standards to ensure the safe operation of aircraft and spacecraft systems.
- Fuel cells: In some aerospace applications, tantalum is used in the construction of fuel cells, which provide an efficient and clean source of electrical power for spacecraft and certain aircraft systems.
- Coating and surface treatments: Tantalum coatings are applied to various aerospace components to enhance their corrosion resistance and wear properties. This can extend the lifespan of critical parts and improve overall system reliability.
- Research and development: The aerospace industry continually explores new applications for tantalum and its alloys in advanced materials research. This includes the development of new high-temperature alloys, composite materials, and innovative manufacturing techniques to push the boundaries of aerospace technology.
The use of Tantalum Ingot in the aerospace industry is driven by the need for materials that can withstand extreme conditions while maintaining high performance and reliability. As aerospace technology continues to advance, with a focus on increasing efficiency, reducing weight, and improving durability, the demand for tantalum and its unique properties is likely to grow. The metal's ability to perform under harsh conditions makes it an invaluable resource in the quest for safer, more efficient, and more capable aircraft and spacecraft.
At SHAANXI CXMET TECHNOLOGY CO., LTD, we take pride in our extensive product range, which caters to diverse customer needs. Our company is equipped with outstanding production and processing capabilities, ensuring the high quality and precision of our products. We are committed to innovation and continuously strive to develop new products, keeping us at the forefront of our industry. With leading technological development capabilities, we are able to adapt and evolve in a rapidly changing market. Furthermore, we offer customized solutions to meet the specific requirements of our clients. If you are interested in our products or wish to learn more about the intricate details of our offerings, please do not hesitate to contact us at sales@cxmet.com. Our team is always ready to assist you.
References
- USGS. (2021). Tantalum. Mineral Commodity Summaries.
- Schwela, U. (2010). The state of tantalum mining. Mining Journal.
- Kock, W., & Paschen, P. (1989). Tantalum—processing, properties and applications. JOM, 41(10), 33-39.
- Ayanda, O. S., & Adekola, F. A. (2011). A review of niobium-tantalum separation in hydrometallurgy. Journal of Minerals and Materials Characterization and Engineering, 10(03), 245.
- Balaji, K., et al. (2015). Tantalum—Review of the metal that's too good to be true. International Journal of Refractory Metals and Hard Materials, 48, 231-237.
- Cardarelli, F. (2008). Materials handbook: a concise desktop reference. Springer Science & Business Media.
- Agulyansky, A. (2004). The chemistry of tantalum and niobium fluoride compounds. Elsevier.
- Okabe, T. H., & Sadoway, D. R. (1998). Metallothermic reduction as an electronically mediated reaction. Journal of materials research, 13(12), 3372-3377.
- Xu, Q., et al. (2019). A review of the manufacture of tantalum powders. Powder Technology, 354, 103-115.
- Peters, M., et al. (2003). Titanium alloys for aerospace applications. Advanced engineering materials, 5(6), 419-427.