Gr16 titanium wire is a specialized alloy commonly used in various industries due to its unique properties. This grade of titanium alloy is known for its excellent combination of strength, corrosion resistance, and biocompatibility. Understanding the composition of Gr16 titanium wire is crucial for engineers, manufacturers, and researchers working with this material. In this blog post, we'll delve into the specific elements that make up Gr16 titanium wire and explore its characteristics and applications.
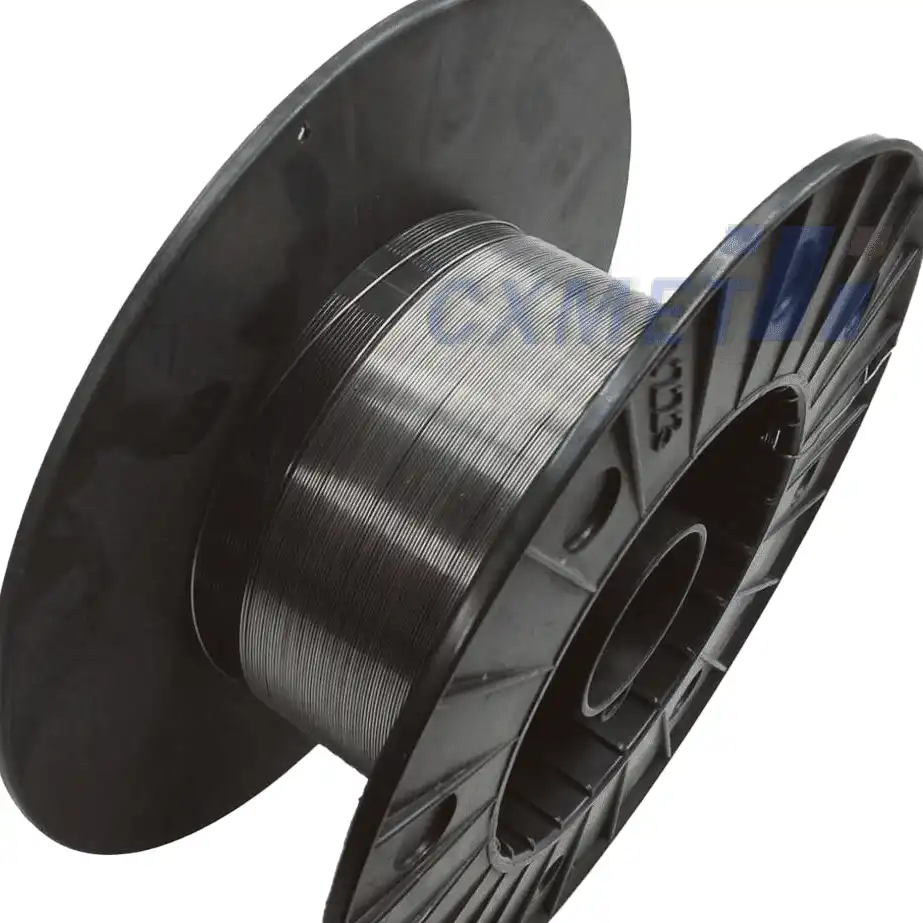
What are the main alloying elements in Gr16 titanium?
Gr16 titanium wire, also known as Ti-6Al-4V ELI (Extra Low Interstitial), is a high-purity variant of the more common Ti-6Al-4V alloy. The main alloying elements in Gr16 titanium are aluminum and vanadium, with strict control over interstitial elements. The composition typically includes:
- Titanium (Ti): 88.1-91% (balance)
- Aluminum (Al): 5.5-6.5%
- Vanadium (V): 3.5-4.5%
- Iron (Fe): 0.25% max
- Oxygen (O): 0.13% max
- Carbon (C): 0.08% max
- Nitrogen (N): 0.05% max
- Hydrogen (H): 0.012% max
- Yttrium (Y): 0.005% max
The "ELI" designation indicates that this alloy has lower levels of interstitial elements (oxygen, nitrogen, carbon, and iron) compared to standard Ti-6Al-4V. This reduction in interstitial elements contributes to improved ductility and fracture toughness, making it particularly suitable for applications requiring high performance and reliability.
The aluminum content in Gr16 titanium wire serves to stabilize the alpha phase of the titanium crystal structure, enhancing strength and reducing density. Vanadium, on the other hand, acts as a beta phase stabilizer, improving the alloy's formability and heat treatment response. The careful balance of these alloying elements results in an optimal combination of strength, toughness, and workability.
The strict control over interstitial elements, particularly oxygen and nitrogen, is crucial for maintaining the alloy's superior mechanical properties. Lower oxygen content leads to improved ductility and fatigue resistance, while reduced nitrogen levels contribute to better fracture toughness. These characteristics make Gr16 titanium wire an excellent choice for critical applications in aerospace, medical, and marine industries.
How does the composition affect the properties of Gr16 titanium wire?
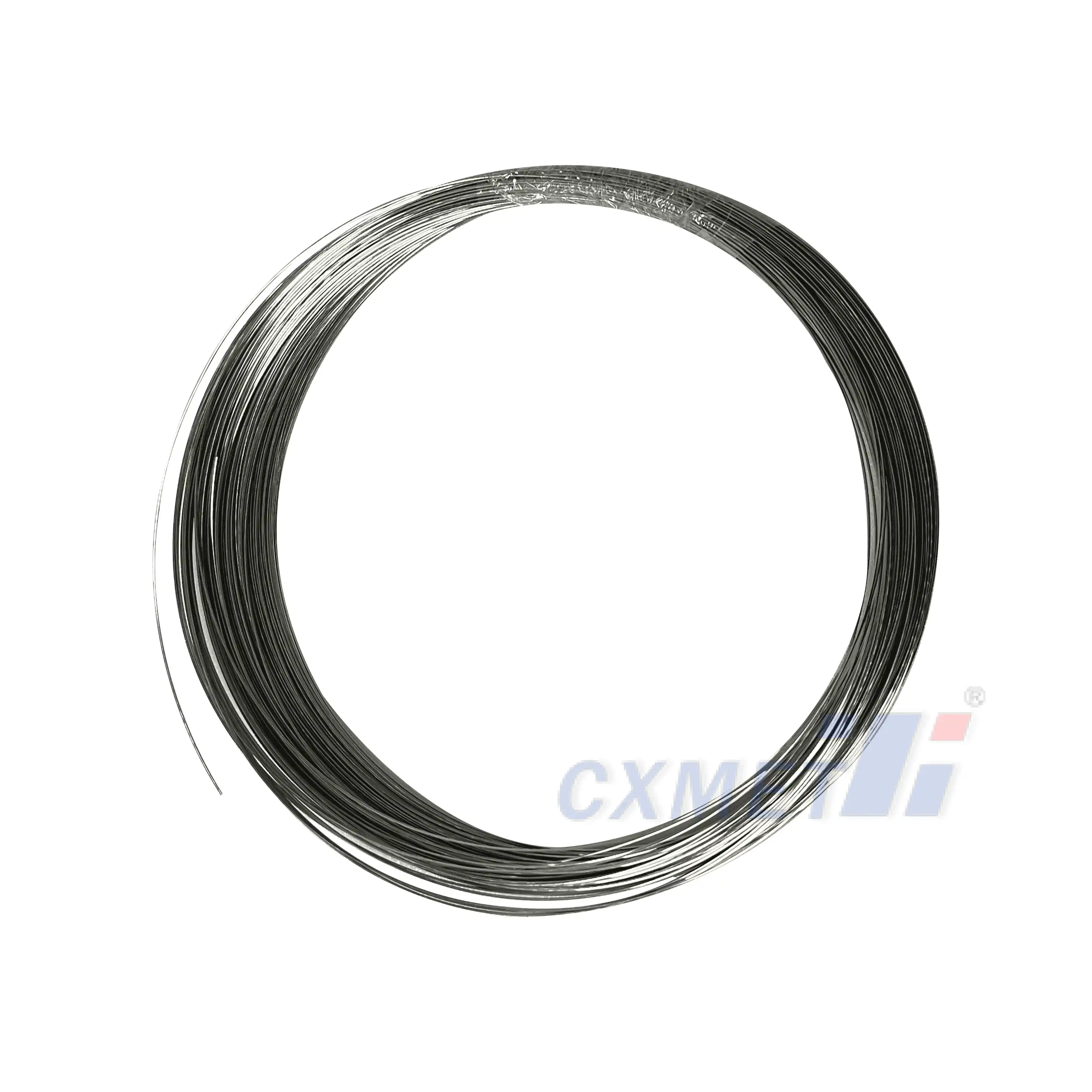
The unique composition of Gr16 titanium wire directly influences its mechanical, physical, and chemical properties. Understanding these relationships is essential for engineers and designers to make informed decisions when selecting materials for specific applications.
Mechanical Properties:
- Tensile Strength: The combination of aluminum and vanadium in Gr16 titanium wire results in a high tensile strength, typically ranging from 860 to 965 MPa. This strength is achieved through solid solution strengthening and the formation of a fine-grained microstructure.
- Yield Strength: Gr16 titanium wire exhibits excellent yield strength, usually between 795 and 875 MPa. This property ensures that the material can withstand high stresses without permanent deformation.
- Elongation: The low interstitial content in Gr16 titanium wire contributes to improved ductility, with elongation values typically ranging from 10% to 15%. This enhanced ductility allows for better formability and resistance to brittle fracture.
- Fatigue Resistance: The composition of Gr16 titanium wire, particularly its low oxygen content, results in superior fatigue resistance. This property is crucial for applications involving cyclic loading, such as aerospace components and medical implants.
Physical Properties:
- Density: The addition of aluminum reduces the overall density of Gr16 titanium wire to approximately 4.43 g/cm³. This low density contributes to the material's high strength-to-weight ratio, making it ideal for weight-critical applications.
- Melting Point: Gr16 titanium wire has a melting point of around 1604-1660°C (2920-3020°F), which is slightly lower than pure titanium due to the alloying elements.
- Thermal Conductivity: The alloy composition results in a thermal conductivity of about 6.7 W/m·K, which is relatively low compared to other metals. This property can be advantageous in applications requiring thermal insulation.
Chemical Properties:
- Corrosion Resistance: The presence of aluminum in Gr16 titanium wire enhances its corrosion resistance by forming a stable, protective oxide layer. This makes the alloy highly resistant to various corrosive environments, including saltwater and bodily fluids.
- Biocompatibility: The low content of interstitial elements, particularly iron and nickel, contributes to the excellent biocompatibility of Gr16 titanium wire. This property is crucial for its use in medical implants and devices.
- Oxidation Resistance: The aluminum content in the alloy improves its oxidation resistance at elevated temperatures, making it suitable for high-temperature applications in aerospace and industrial settings.
The unique combination of these properties, derived from its carefully controlled composition, makes Gr16 titanium wire an exceptional material for a wide range of demanding applications. Its high strength-to-weight ratio, excellent corrosion resistance, and biocompatibility have led to its widespread use in aerospace, medical, and marine industries, where performance and reliability are paramount.
What are the main applications of Gr16 titanium wire?
The exceptional properties of Gr16 titanium wire, resulting from its unique composition, make it a versatile material with applications across various industries. Its combination of high strength, low density, excellent corrosion resistance, and biocompatibility opens up a wide range of possibilities for engineers and designers. Let's explore some of the main applications of Gr16 titanium wire:
Aerospace Industry:
- Structural Components: Gr16 titanium wire is used in the fabrication of critical aerospace structures, such as fuselage frames, wing spars, and engine mounts. Its high strength-to-weight ratio allows for weight reduction while maintaining structural integrity.
- Fasteners: The alloy is commonly used to produce high-strength fasteners, including bolts, nuts, and rivets, for aircraft assembly. These fasteners benefit from the material's corrosion resistance and fatigue strength.
- Landing Gear Components: The superior fatigue resistance and strength of Gr16 titanium wire make it an excellent choice for landing gear parts, which undergo significant stress during takeoff and landing.
- Hydraulic and Pneumatic Systems: The alloy's corrosion resistance and strength make it suitable for tubing and fittings in aircraft hydraulic and pneumatic systems.
Medical Industry:
- Implants: Gr16 titanium wire is extensively used in the production of various medical implants, including hip and knee replacements, dental implants, and spinal fixation devices. Its biocompatibility and osseointegration properties make it ideal for long-term implantation.
- Surgical Instruments: The material's strength, lightness, and ability to withstand repeated sterilization make it suitable for manufacturing surgical instruments and tools.
- Cardiovascular Devices: Gr16 titanium wire is used in the production of heart valve components, stents, and pacemaker leads, taking advantage of its biocompatibility and fatigue resistance.
- Prosthetics: The alloy's strength and low weight make it an excellent choice for prosthetic limbs and components, improving comfort and functionality for users.
Marine Industry:
- Propulsion Systems: Gr16 titanium wire is used in marine propellers and propulsion system components due to its excellent corrosion resistance in saltwater environments.
- Heat Exchangers: The alloy's resistance to corrosion and erosion makes it suitable for heat exchanger tubing in desalination plants and offshore platforms.
- Underwater Equipment: Gr16 titanium wire is used in the construction of deep-sea exploration equipment, submersibles, and ROVs (Remotely Operated Vehicles) due to its strength and corrosion resistance at high pressures.
- Marine Fasteners: The material is used for bolts, nuts, and other fasteners in marine applications where corrosion resistance is critical.
Chemical Processing Industry:
- Pressure Vessels: Gr16 titanium wire is used in the fabrication of pressure vessels and tanks for handling corrosive chemicals and gases.
- Heat Exchangers: The alloy's corrosion resistance makes it suitable for heat exchanger tubing in chemical processing plants.
- Piping Systems: Gr16 titanium wire is used to produce pipes and fittings for transporting corrosive fluids in chemical plants.
Sports and Leisure:
- Golf Club Heads: The material's high strength-to-weight ratio and excellent elasticity make it ideal for manufacturing golf club heads.
- Bicycle Frames: High-end bicycle frames benefit from the alloy's strength, lightness, and fatigue resistance.
- Sports Equipment: Gr16 titanium wire is used in various sports equipment, including tennis rackets, climbing gear, and high-performance skis.
Energy Industry:
- Geothermal Wells: The alloy's corrosion resistance in high-temperature, high-pressure environments makes it suitable for geothermal well components.
- Offshore Oil and Gas: Gr16 titanium wire is used in various offshore applications, including risers, heat exchangers, and subsea equipment, due to its corrosion resistance in marine environments.
The versatility of Gr16 titanium wire, stemming from its carefully engineered composition, continues to drive innovation across these industries. As research and development progress, new applications for this exceptional alloy are likely to emerge, further expanding its use in cutting-edge technologies and demanding environments.
At SHAANXI CXMET TECHNOLOGY CO., LTD, we take pride in our extensive product range, which caters to diverse customer needs. Our company is equipped with outstanding production and processing capabilities, ensuring the high quality and precision of our products. We are committed to innovation and continuously strive to develop new products, keeping us at the forefront of our industry. With leading technological development capabilities, we are able to adapt and evolve in a rapidly changing market. Furthermore, we offer customized solutions to meet the specific requirements of our clients. If you are interested in our products or wish to learn more about the intricate details of our offerings, please do not hesitate to contact us at sales@cxmet.com. Our team is always ready to assist you.
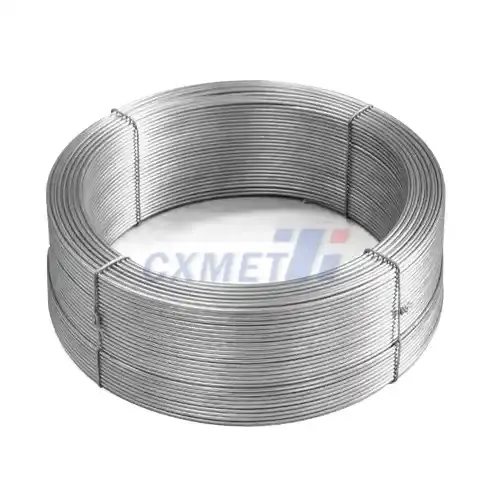
References
- ASTM International. (2021). ASTM F136-13 Standard Specification for Wrought Titanium-6Aluminum-4Vanadium ELI (Extra Low Interstitial) Alloy for Surgical Implant Applications (UNS R56401).
- Boyer, R., Welsch, G., & Collings, E. W. (1994). Materials Properties Handbook: Titanium Alloys. ASM International.
- Donachie, M. J. (2000). Titanium: A Technical Guide. ASM International.
- Froes, F. H. (2015). Titanium: Physical Metallurgy, Processing, and Applications. ASM International.
- Leyens, C., & Peters, M. (Eds.). (2003). Titanium and Titanium Alloys: Fundamentals and Applications. John Wiley & Sons.
- Lütjering, G., & Williams, J. C. (2007). Titanium. Springer Science & Business Media.
- Peters, M., Hemptenmacher, J., Kumpfert, J., & Leyens, C. (2003). Structure and Properties of Titanium and Titanium Alloys. Titanium and Titanium Alloys: Fundamentals and Applications, 1-36.
- Rack, H. J., & Qazi, J. I. (2006). Titanium alloys for biomedical applications. Materials Science and Engineering: C, 26(8), 1269-1277.
- Titanium Industries. (2021). Ti-6Al-4V ELI (Grade 23). Retrieved from https://www.titanium.com/titanium-grade-23-6al-4v-eli/
- Veiga, C., Davim, J. P., & Loureiro, A. J. R. (2012). Properties and applications of titanium alloys: A brief review. Reviews on Advanced Materials Science, 32(2), 133-148.